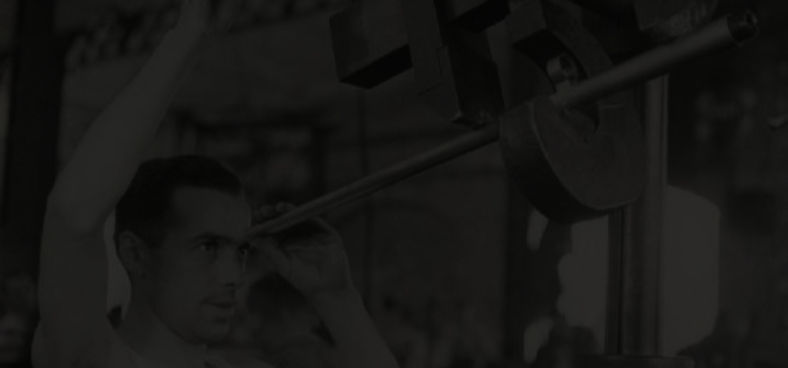
COLLAUDO ARMI
INTRODUZIONE
Molte persone (Soprattutto oltreoceano) nel corso degli ultimi decenni hanno trattato i Carcano come bombe a orologeria, considerandoli spazzatura, costruiti da una "cultura tecnica" inferiore (per usare termini politicamente corretti), creando così leggende di lunga durata su tolleranze calcolate a casaccio, "canne strette", problemi di headspace, assemblaggi di pessima qualità che porterebbero a scarsa precisione, e così via.
Un altro mito che dura da tempo è che l'Italia abbia adottato la "semplice" azione Carcano perché il Paese non poteva permettersi, sia economicamente che a livello tecnico e industriale, qualcosa di più complesso.
Si tratta fondamentalmente di leggende alimentate oltreoceano prevalentemente da pregiudizi "culturali" (vedi sopra); il problema è che poi molti tiratori nostrani si sono adeguati ai mantra e alle esagerazioni americane, spandendo a loro volta leggende metropolitane degne dei peggiori baretti di quartiere.
Spero che riportando alcuni dei processi industriali impiegati nella produzione di queste armi avrò modo di aiutare i collezionisti a comprendere al meglio la verità su queste armi così bisfrattate.
CONTESTO STORICO
L'Italia ha adottato l'azione del Cav. Salvatore Carcano, unita al sistema di alimentazione Mannlicher, esclusivamente sulla base di un rapporto qualità/costo-efficacia, non "perché è quello che si era in grado di costruire". Certamente il budget era una questione fondamentale, ma come lo era in ogni nazione industrialmente avanzata.
L'azione offerta da Salvatore Carcano era robusta, affidabile, efficace, facile da smontare e funzionava senza grossi problemi. Il sistema di alimentazione offerto dal serbatoio Mannlicher è stato visto come il miglior compromesso possibile per la ricarica dell'arma, e così la commissione e i tecnici delle Regie Fabbriche d'Armi fecero del loro meglio per far funzionare insieme i due sistemi al meglio.
Per quanto riguarda le leggende riguardanti una "lavorazione scadente", bisogna tenere presente che le nazioni povere non possono permettersi di avere armi mal costruite, inprecise o potenzialmente pericolose: se devi spendere soldi, le tue armi devono essere impeccabili e durare il più possibile e nel modo più efficente possibile.
Ecco perché la produzione e il controllo qualità dei Fucili e moschetti Carcano sono stati assolutamente rigorosi e dettagliati, fino all'ultima vite.
COLLAUDO GENERALE
Il controllo di qualità per tutti i fucili prodotti seguiva i seguenti passaggi:
I - PRODUZIONE E VERIFICA PARTI
Tutte le parti del fucile venivano costantemente ispezionate durante la produzione, sia dai capi operai prima, sia dai Capi Tecnici (CT) quando le parti erano pronte.
Se il Capo Tecnico rilevava che la singola parte rientrava nelle tolleranze specifiche della produzione, la contrassegnava con le sue iniziali e la inviava al Laboratorio di Controllo e Verifica.
Negli Arsenali erano presenti diversi capi tecnici, ciascuno responsabile di una specifica linea di produzione.
Ad esempio, a Terni nel 1914 esistevano 8 officine/laboratori:
- 1° Laboratorio - produzione pistole lanciarazzi e proiettili da 75 mm, oltre a parti di macchinari - CT Barillaro Bruno
- 2° Laboratorio - produzione otturatori, caricatori, gruppi di scatto/grilletti, minuterie - CT Moretti Silvio
- 3° Laboratorio - produzione Canne e Culatte - CT Salerno Giuseppe & Lucchi Giorgio
- 4° Laboratorio - produzione calciature e astine paramano in legno - CT Galbardi Giovanni Battista
- 5° Laboratorio - Fonderia - nessun CT
- 6° Laboratorio - produzione Baionette e Molle elicoidali, trattamenti termici - CT Moschini Ettore
- Servizi generali - Manutenzione generale dell'arsenale - CT Mirabelli Luigi
- Laboratorio di Controllo e collaudo - CT Galbardi Santo
Dettaglio sulla produzione delle Canne:
Tutte le canne prodotte venivano testate con 3 colpi che sviluppavano ciascuno una pressione di circa 4000 atm (60k psi);
Superata questa prova venivano marcate con Anno, Produttore, Provenienza dell'Acciaio della sbarra da cui era stata ottenuta (Sigla dell'acciaieria).
Da ogni lotto di canne prodotte e testate, lo 0,2% delle canne (quindi su 10.000, solo 20) venivano ulteriormente testate con 5 cartucce speciali, sviluppando dalle 4300 alle 5500 atm (da 63k a 80k psi); ciascuna cartuccia aumentava la pressione massima di 300 atm (4.400psi).
I proiettili dovevano mantenere la velocità del proiettile alla volata entro le specifiche e se anche una sola canna si crepava, anche solo leggermente, l'intero lotto doveva essere scartato.
II - LABORATORIO DI CONTROLLO E COLLAUDO
Prima di essere spediti al laboratorio di assemblaggio, tutti i pezzi prodotti venivano inviati al Laboratorio di Controllo e Collaudo, dove veniva nuovamente esaminato approfonditamente il 10% di ogni lotto di parti prodotto.
Se ispezionando e misurando una componente si fossero verificate ripetutamente delle incongruenze rispetto alle specifiche di produzione, un altro 10% del lotto di quella parte specifica sarebbe stato ispezionato e, se i problemi fossero persistiti, l'intero lotto sarebbe stato rispedito al laboratorio per essere completamente rielaborato.
Le parti accettate ottenevano un ulteriore marchio di approvazione: in particolare le culatte, gli otturatori, i serbatoi, bocchini e fascette. Successivamente Tutte le parti approvate venivano inviate al laboratorio di assemblaggio, che procedeva ad assemblare le armi, senza astina paramano, per essere pronte per il collaudo.
III - PROVA FORZATA DI ARMA COMPOSTA
Ogni singolo fucile assemblato veniva sottoposto alla Prova Forzata di Arma composta: sostanzialmente si sparava una cartuccia specifica (Cartuccia per Prova Forzata) progettata per sviluppare pressioni superiori del 25% alla pressione massima della cartuccia militare, seguita da due cartucce normali.
Poiché le cartucce caricate con Solenite sviluppavano circa 3200 atm (47k psi), la cartuccia per prova forzata fu progettata per sviluppare oltre 4000 atm (60k psi).
Prima del 1912 la cartuccia per Prova Forzata sarebbe dovuta essere progettata per sviluppare circa 5000 atm, poiché la pressione massima della cartuccia militare caricate a balistite era di circa 4000 atm.
Se dopo questa prova l'arma ciclizzava regolarmente e le sue misure di camera ed headspace rientravano nelle specifiche, la canna veniva marchiata con il marchio di prova dello Scudo Sabaudo e rispedite al laboratorio di assemblaggio, che le smontava e le puliva per i controlli finali.
Questi consistevano nel controllare che:
- La canna fosse dritta come prima della prova forzata
- Le mire fossero allineate al piano mediano della canna, l'alzo fosse conforme alle specifiche
- Tutte le parti si incastrassero senza gioco e senza essere troppo strette
- La canna appoggiasse correttamente nell'incasso della calciatura
- I movimenti dell'otturatore fossero fluidi e l'headspace fosse corretto
- L'elevatore del caricatore si muovesse bene
- Il gruppo di scatto/Grilletto venisse attivato tra gli 1,5 e 2,5 kg (3,3-5,5 libbre) di pressione
- Estrattore ed espulsore funzionassero perfettamente, la lastrina cadesse liberamente dal fondo del caricatore
- La baionetta si inserisse e si rimuovesse facilmente con una sola mano e si incastrasse nel suo attacco correttamente, senza oscillare troppo.
- L'Astina Paramano si adattasse correttamente alla canna, mantenuta in posizione dalla fascetta e dal taglio per la tacca di mira ripiegata
- Il fucile non avesse tagli o colpi, corrispondendo alle aspettative estetiche.
A questo punto le armi venivano rimontate definitivamente e il loro numero di matricola veniva impresso sia sulla canna che sulla pala del calcio, per poterle ritrovare facilmente sulle rastrelliere delle caserme.
Tutte le armi venivano poi inviate alla Commissione di Collaudo
COMMISSIONE DI COLLAUDO
La Commissione di Collaudo era incaricata di testare a campione i lotti giornalieri di armi complete fornite dal laboratorio di assemblaggio.
Il primo passaggio intrapreso dalla commissione era di prendere un fucile completamente a caso e controllare nei minimi dettagli che ogni singola parte rientrasse nelle specifiche e tolleranze di costruzione. Ciò veniva fatto principalmente per verificare se gli strumenti e attrezzi delle officine rientrassero ancora nei parametri operativi o se necessitavano di una sostituzione.
Successivamente il 10% delle armi veniva inviato alla Prova di Esattezza; questo 10% veniva diviso per 100 gruppi di armi, in base al prefisso seriale; di questi 100, 10 armi venivano testate direttamente.
Su una produzione giornaliera di 1000 fucili, c'era solo un gruppo di 100 armi da testare, ma quando la produzione raggiunse le 2500 armi giornaliere, c'erano 2 gruppi e mezzo da ispezionare al giorno.
I 10 fucili testati venivano posizionati e fissati su un cavalletto, la canna veniva pulita accuratamente, il fucile puntato a 28 cm sotto il centro del bersaglio posto a 200 m di distanza (il tutto mirando con tacca di mira fissa, tarata a 300 m) in modo che i proiettili colpissero, almeno a livello teorico, il centro del bersaglio.
Successivamente venivano sparate 6 cartucce militari prese a caso e, affinché l'arma fosse approvata, i proiettili avrebbero dovuto rispettare le seguenti specifiche:
- Il centro della rosata non deve discostarsi dal centro del bersaglio di 20 cm in orizzontale e 25 cm in verticale;
- La deviazione verticale media (media delle deviazioni verticali di ogni singolo proiettile dal centro della rosata) non deve superare i 6 cm, mentre la deviazione laterale media non deve superare i 5 cm. A 200 m, ciò si traduce in circa 2 MOA.
Se solo 1 dei 10 fucili testati non riusciva a raggiungere questi risultati, veniva approvato l'intero gruppo di 100 armi.
Se 2 o più dei 10 fucili testati non riuscivano a raggiungere questi risultati, altri 20 fucili dei 100 originali venivano prelevati e testati, insieme ai primi 10.
Se solo 2 di questi 30 fucili testati non riuscivano a raggiungere questi risultati, veniva approvato l'intero gruppo di 100 armi.
Se 3 o più fucili invece non riuscivano ancora a raggiungere questi risultati, l'intero lotto veniva testato e tutti i singoli fucili difettosi venivano rimandati alle linee di produzione per essere revisionati.
L'intero lotto di 100 armi omologate veniva poi marchiato con il marchio dei Fucili Incrociati ed inviato ai successivi collaudi.
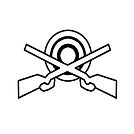
Nei test successivi i 100 fucili venivano:
- Smontati e puliti
- Il calibro della canna veniva controllato con i verificatori Accettazione Fabbrica / Rifiuto Servizio (Go/No-go)
- Le scanalature della canna venivano controllate con i verificatori Accettazione Fabbrica / Rifiuto Servizio (Go/No-go)
- La camera veniva controllata con i verificatori Accettazione Fabbrica / Rifiuto Servizio (Go/No-go)
- L'headspace veniva controllato con i verificatori Accettazione Fabbrica / Rifiuto Servizio (Go/No-go)
- I mirini venivano controllati per verificare se erano nella posizione corretta e allineati
- Il gruppo discatto veniva controllato per vedere se la forza di trazione rientrava nelle specifiche
- Il percussore veniva controllato per vedere se rientrava nelle specifiche (1,4-1,6 mm sporgenti dalla testa dell'otturatore)
- Veniva controllato l'allineamento tra ricevitore e caricatore
- La molla dell'elevatore veniva controllata per vedere se rientrava nelle specifiche di fabbricazione
- Veniva verificata l'intercambiabilità della Baionetta
Se in questi test venivano riscontrati diversi problemi rilevanti, le prove venivano estese a tutti i fucili di quel lotto, e quelli difettosi venivano rispediti alle linee di produzione per essere completamente revisionate.
L'ultima prova del Comitato di Accettazione era la prova di intercambiabilità delle parti, applicata sul 5% delle armi selezionate: tutte queste armi venivano completamente smontate, ad eccezione delle mire, delle componenti interne del serbatoio e del percussore (che in realtà è in due parti, tenute insieme da una spina), le parti sono state mescolate e le pistole riassemblate con parti scelte a caso.
Tutti i fucili venivano quindi controllati e testati con verificatori AF/RS (Go/No-Go) per vedere se tutto rientrava nelle specifiche di servizio.
Se anche un solo fucile non rientrava nelle specifiche, l'intero lotto veniva rimandato alle linee di produzione per la revisione.
Tutte le armi accettate venivano poi marchiate con i marchi di approvazione definitiva, lubrificate e messe in deposito.
PROVA DI DURATA
Mentre proseguivano le altre prove, un singolo fucile per ogni lotto matricolare di 10.000 veniva sottoposto a una prova di durata, altresì nota all'epoca come Spirto di Cimento:
Il 2500 cartucce (poi aumentate a 4000) provenienti da diversi anni di produzione (solitamente i tre anni precedenti) venivano sparate con il suddetto fucile.
Il test consisteva nel sparare 50 colpi per sessione di tiro, controllando l'erosione della canna ogni 250 colpi.
Alla fine del test, il calibro Rifiuto Servizio (No-Go, 6,65mm) per il calibro della canna non avrebbe dovuto scendere nella gola della canna per più di 2 cm, indicando che il fucile era ancora (almeno sulla carta) utilizzabile con successo.
Se l'arma non rispettava queste specifiche venivano testati altri 2 fucili. Se solo uno dei due fucili in più non rispettava queste specifiche, l'intero lotto di 10.000 fucili veniva rifiutato.
PRIVATE INDUSTRY
PRODUCTION REQUIREMENTS
Guns produced by private firms, like M.I.D.A., F.N.A. and Beretta had to be tested by army inspectors, using army instruments and tools.
So every single part of rifles and carbines produced by private industries must conform to the Army specs, especially interchangeability wise.
The testings, expleted by the Acceptance Committee (Commissione di Collaudo), were exactly the same the committee applied in the arsenals, but even more stricts in term of rejected complete guns: if even a single assembled guns didn't pass one single test of the Acceptance Commitee process, the whole batch was refused and had to be refurbished.
Only the Firing test (18 rounds fired, bullets shouldn't keyhole) and the Accuracy testing (Prova di Esattezza) were more lax, since they followed the arsenals requirements: if 3 on 30 guns had issues in only one of these tests, the whole batch was refused.
Even worst for private firms, every additional test with the refused batch (once refurbished) could have been done only two more times. And every extra test (ammo and inspector's fees) had to be charged on the firm itself.
The Acceptance Committee also performed a Velocity test (bullet should have muzzle velocity within specs) and the Endurance test ( 4000 rounds fired, Caliber No-go gauge shouldn't go further than 2cm into the barrel, Bolt won't close on a No-Go gauge)
All accepted guns were approved (after 1934) with the crowned R.E. marking.