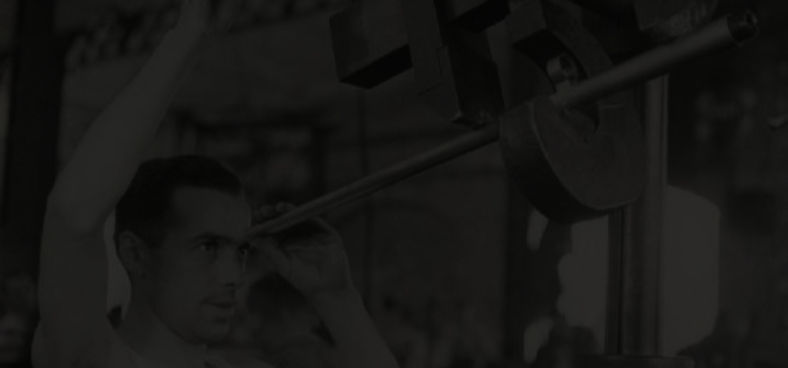
QUALITY CONTROL
INTRODUCTION
Lots of people along the decades treated Carcanos as ticking time bombs, considering them junk, built by an inferior "technical culture" (to use gentle terms), thus creating long lasting fudd lores about loose tolerances, "tight barrels", headspace issues, terrible assembly leading to poor precision, so on and so forth. Another long lasting myth is that Italy adopted the "simple" Carcano action because the country couldn't afford, both economically and on a technical and industrial level, anything more complex.
These are basically fudd lores fueled mostly by "cultural" biases, and I hope that by explaining some of the industrial processes involved in these guns production I can help collectors getting a hold of the truth.
HISTORICAL CONTEXT
Italy adopted the Carcano action over a Mannlicher magazine exclusively upon a quality/cost effectiveness ratio, not "because that's what they could build". Certainly budget was on the line, but as it was on the line in every industrial nation.
The action offered by Salvatore Carcano was sturdy, reliable, effective in action, easy to disassemble and worked without big issues. The feeding system offered by the Mannlicher magazine was seen as the best possible compromise, and so they made the two parts work together the best they could.
As for the "poor craftmanhip" you have to keep in mind that poor nations can't really afford to have poorly constructed, accurate or potentially dangerous guns: if you have to spend money, your guns must be flawless and last as much as possible and as effectively as possible.
That's why Carcanos' manufacture and quality control was absolutely strict and detailed, to the last screw.
STANDARD QUALITY CONTROL
The Standard Quality control for all produced Fucili mod.91 followed these specific steps:
I - PARTS PRODUCTION AND TESTING
Small parts were constantly kept under scrutiny, both by the workers supervisors first and by the Chief Technicians (CT) when the parts were ready.
​If the Chief Technician decided that the individual part was within specs, he marked it with his initials.
There were several chief technicians in the Arsenals, each responsible of a specific production line.
For instance, in Terni in 1914 there were 8 workshops/laboratories:
- 1st Laboratory - producing Flare pistols and 75mm shells, along with machineries - CT Barillaro Bruno
- 2nd Laboratory - producing Bolts, magazines, trigger groups, metal parts - CT Moretti Silvio
- 3rd Laboratory - producing Barrels and Receivers - CT Salerno Giuseppe & Lucchi Giorgio
- 4th Laboratory - producing wooden Stocks and handguards - CT Galbardi Giovanni Battista
- 5th Laboratory - Foundry - no CT
- 6th Laboratory - producing Bayonets and springs, heat treating parts - CT Moschini
- General services - General Maintenance of the arsenal - CT Mirabelli Luigi
- Control and Testing Laboratory - CT Galbardi Santo
Detail about the production of barrels:
All barrels produced got tested with 3 rounds, each developing 4000 atm (60k psi);
After this test the barrels got marked with manufacturer, year and with the code indicating the steel mills that produced the original steel bar.
​From each produced and tested barrel batch, 0,2% of the barrels (so out of 10,000, only 20) got further tested with 5 special cartridges, developing 4300 to 5500 atm (63k to 80k psi), each cartridge increasing by 300 atm (4.400 psi).
During this test, bullets should mantain the muzzle velocity within the predicted specs, and if a single barrel cracked, even slightly, the whole batch had to be discarded.
II - CONTROL AND TESTING LABORATORY
Before being shipped to the assembly laboratory, parts were sent to the Control and Testing Laboratory, where 10% of each daily produced batch of small parts got thorough examined, again.
If there were some issues on a specific part inspected, another 10% of that part batch would have been inquired, and if the issues persisted, the whole batch was sent back to the laboratory to be completely reworked.
Accepted parts got an extra mark of approval, especially receivers, bolts, magazines and barrel bands. Then they were all sent to the assembly laboratory, that proceeded in assembling the guns, without the handguard, in order to be ready for the prooftest.
III - PROOFTESTING
Every single assembled gun got prooftested with a Forced Test cartridge, basically a specific cartridge designed to develop 25% pressures above the av max pressure of the military cartridge, followed by two regular cartridges.
Since Solenite loaded cartridges developed about 3200 atm (47k psi) the forced cartridge was designed to develop 4000+ atm (60k psi).
Before 1912 the Forced Test cartridge was designed to develope about 5000 atm since the av max pressure of the balistite military cartridge was about 4000 atm.
If the gun cycled flawlessly and was within the previous specs, the barrel got marked with the crowned shield proofmark, and sent back to the assembly laboratory that dismounted and cleaned them for the final checks, consisting in:
- Barrel is straight as before the prooftest
- Sights are aligned in the middle of the barrel, Rear sight is in spec
- all parts fit without game and without being too tight
- Barrel rest correctly on the stock bedding
- Bolt movements are smooth and headspace correct
- Magazine elevator move fine
- Trigger group is activated within 1,5 and 2,5kg (3,3-5,5 lbs) of pressures
- Extractor and expulsor work flawlessly, clip falling freely from the bottom of the magazine
- Bayonet is easily inserted and removed with a single hand, and fit correctly without wobbling
- handguard fit correctly the barrel, kept in position by the barrel band and cut for the folded rear sight
- Gun is aestethically fitting the expectations.
At this point guns were reassembled definitively and their serial number impressed both on the barrel and on the stock, in order to find them easily on racks, and sent to the Acceptance committee
ACCEPTANCE COMMITTEE
The Acceptance Commitee (Commissione di Collaudo) was in charge of randomly testing the daily batches of complete guns.
First step was taking a completely random rifle and checking in absolute detail that every single part was within specs. This was made mostly to check if the workshop tools and instruments were still within specs themselves, or if they needed an update or refurbishment.
Then 10% of the guns was sent to the Accuracy Testing (Prova di Esattezza); these got divided by 100 gun groups according to the serial prefix, and of these 100, 10 got directly tested. On a daily production of 1000 rifles, there was only one group of 100 to test, but when the production reached 2500 daily guns, there were 2 groups and a half to inspect.
The 10 guns tested were put and secured on a stand, barrel was cleaned thorough, gun was pointed 28cm under a target 200m away (with fixed 300m battle sight) so that bullets would hit the bullseye of the target.
Then 6 standard cartridges were shot, and, for the gun to be approved the bullets should have respected the following specs:
- The Center of the Grouping shouldn't deviate from the center of the target 20cm (8") horizontally and 25cm (10") vertically;
- Average Vertical Deviation (Average sum of each single bullet vertical deviations from the grouping center) shouldn't exceed 6cm, while Average lateral Deviation shouldn't exceed 5cm. At 200m, that translates in about 2 MOA
If only 1 of the 10 guns tested didn't manage to reach these results, the whole 100 group of gun was approved.
If 2 or more of the 10 guns tested didn't manage to reach these results, another 20 guns from the original 100 were picked up and tested, along with the first 10. If only two of these 30 guns tested didn't manage to reach these results, the whole 100 group of gun was approved. If 3 or more guns were still unable to reach these results, the whole batch was tested and all the faulty guns were sent back to the production lines to be overhauled.
The whole lot of 100 guns approved was then marked with the Crossed Rifles marking and sent to the next testings.
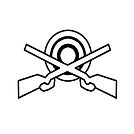
In the next testings the 100 guns got:
- Disassembled and cleaned
- Barrel caliber got checked with the Go/No-Go gauges
- Barrel grooves got checked with the Go/No-Go gauges
- Chamber got checked with the Go/No-Go gauges
- Headspace got checked with the Go/No-Go gauges
- Sights got checked to find if they were in the correct position and aligned
- Trigger group got checked to see if the pull force was within specs
- Firing pin got checked to see if it was within specs (1,4-1,6 mm exposed)
- Alignment between receiver and magazine got checked
- Elevator spring got checked to see if it was within specs
- interchangeability of the Bayonet was checked
If in these testings several relevant issues were found, the testing was extende to all the guns of that serial prefix batch, and the faulty ones were sent back for overhaul
​The last Acceptance Commitee test was the parts interchangeability test, applied on 5% of the guns selected: all these guns were completely disassembled, except for the Sights, the magazine internals and the firing pin (that it's actually in two parts, kept in place by a pin), parts were mixed and guns reassembled with randomly picked parts.
All the guns were then checked and tested with Go/No-Go gauges to see if everything was within service specs.
If even only a single gun wasn't within specs, the whole 100 guns batch was sent back to the production lines for overhauling.
All accepted guns got then marked with the final approvance markings, greased and put in storage.
ENDURANCE TEST
While the other tests were going on, one single rifle for each 10,000 batch got tested for an endurance test:
The Rifle was shot with 2500 cartridges (then increased to 4000) from different years of productions (usually the previous three years).
The testing consisted in shooting 50 rounds per session, checking the barrel erosion after every 250 rounds.
At the end of the test, the No-Go gauge for barrel caliber (6,65mm) shouldn't have gone down the throat of the barrel for more than 2cm, indicating that the gun was still (Barely) serviceable.
If the gun didn't respect these specs, another 2 rifles were tested. If only one of these two extra rifles didn't respect these specs, the whole, entire batch of 10,000 guns was refused.
PRIVATE INDUSTRY
PRODUCTION REQUIREMENTS
Guns produced by private firms, like M.I.D.A., F.N.A. and Beretta had to be tested by army inspectors, using army instruments and tools.
So every single part of rifles and carbines produced by private industries must conform to the Army specs, especially interchangeability wise.
​
The testings, expleted by the Acceptance Committee (Commissione di Collaudo), were exactly the same the committee applied in the arsenals, but even more stricts in term of rejected complete guns: if even a single assembled guns didn't pass one single test of the Acceptance Commitee process, the whole batch was refused and had to be refurbished.
Only the Firing test (18 rounds fired, bullets shouldn't keyhole) and the Accuracy testing (Prova di Esattezza) were more lax, since they followed the arsenals requirements: if 3 on 30 guns had issues in only one of these tests, the whole batch was refused.
Even worst for private firms, every additional test with the refused batch (once refurbished) could have been done only two more times. And every extra test (ammo and inspector's fees) had to be charged on the firm itself.
The Acceptance Committee also performed a Velocity test (bullet should have muzzle velocity within specs) and the Endurance test ( 4000 rounds fired, Caliber No-go gauge shouldn't go further than 2cm into the barrel, Bolt won't close on a No-Go gauge)
All accepted guns were approved (after 1934) with the crowned R.E. marking.